With some of the world’s most prominent car manufacturers announcing plans to phase out petrol and diesel-powered vehicles entirely within the next decade and a half, electric vehicles (EVs) are no longer a dream of the future.
General Motors in the US have stated their intentions to sell only EVs by 2035, while the global growth in sales of EVs and President Biden’s pledge to reach 50% electrification by 2030 prove that EV adoption is finally reaching the mainstream.
This rapid growth, and the move away from fossil fuel reliance, is generally seen as a positive, however, this is not the end of the story, and the social and environmental concerns around how to dispose of lithium batteries that EVs are usually powered by are now coming to light.
The lithium car battery issue is twofold. First, there is clear concern around the level of virgin raw material mining needed for their manufacture. This reliance on metals and minerals as the foundation of this technology presents significant environmental and social issues. However, there are now increased efforts to reduce this through the development of new technologies.
The other problem is, of course, how to dispose of lithium car batteries once they have reached the end of their useful lives—an issue compounded by the types of materials used during manufacture. Today, you can recycle lithium car batteries, and this is the best way to minimize the mining of new raw materials, however, they are not as easily recycled as more conventional lead-acid batteries usually found in cars.
This means that regulators, manufacturers, and other industry players are now attempting to find the best ways to maximize the efficiency of lithium car battery recycling. However, there are numerous barriers to effectively recycling lithium car batteries, some of which we explore here.
How do Lithium Car Batteries Work?
Most electric vehicles run on lithium-ion batteries. Each cell of a lithium battery generates electricity when its lithium ions move from one side (the anode) through an electrolyte to the other side (the cathode). The lithium in the anode is cheap and ubiquitous, although its extraction is not without its issues, however, the cathode contains valuable metals like nickel, manganese, and cobalt, on which the performance of the battery heavily relies.
It is the mining of these precious metals that has a greater environmental and social impact; for example, in fueling conflict and child labour in metal-rich countries like the Democratic Republic of Congo, where almost two-thirds of the world’s cobalt mining takes place.
Because of these concerns, researchers have focused on finding ways to phase out cobalt use in lithium batteries. There has been some success; start-up TexPower in the US has found an effective way of cutting out cobalt without compromising on efficacy, while EV trailblazer Tesla plans to stop using cobalt altogether over the next few years.
But while these raw material developments make the manufacture of lithium-ion batteries more sustainable, the impact on recycling is less straightforward.
Are Lithium Car Batteries Recyclable?
Although lithium car batteries are recyclable, it is a costly and energy-intensive process. One significant setback is the modular composition of the battery cells within a battery pack. The cells are welded and glued together with such solidity that breaking them down requires a lot of human or machine power and emits greenhouse gasses along the way.
Most commonly, lithium batteries are recycled in large plants by a process of shredding the whole battery down to a powder. This powder is then either smelted (pyrometallurgy) or dissolved in acid (hydrometallurgy), thereby extracting the individual elements for resale.
One problem with this process is that when you remove the scarce, expensive metals like cobalt from the battery, the recycling industry is left with a lower value product to resell. Lithium is so cheap to mine so there’s no incentive to recycle the lithium in car batteries. Ironically, removing controversial elements like cobalt from the battery makes the process less worthwhile for companies that recycle lithium car batteries.
What Are the Solutions to Lithium Car Battery Recycling?
If lithium car battery recycling isn’t yet profitable, that doesn’t mean it won’t be as the industry scales up, but to get there the recycling technology and the batteries themselves must continue to develop. This is where incentivization plays a part.
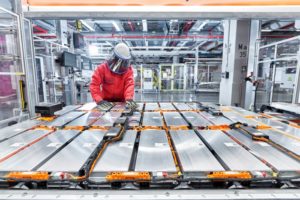
Source: nature.com
The concept of Extended Producer Responsibility, in which a manufacturer is considered liable for the impact of their product throughout its entire lifecycle, has been key to the strides made in this direction. In China, where much of the world’s battery manufacture is found, the state has taken steps to place the responsibility of lithium car battery disposal back on the makers. Chinese battery manufacturers now have clear financial and regulatory incentives to source recycled materials over mining fresh ones.
Additionally, these measures have compelled manufactures to find ways to design batteries to make the recycling process more efficient at the other end. One Chinese company, BYD, has begun to develop a new kind of battery pack, the blade, which moves away from the modular build for a flat pack battery and created a product free from the glues and adhesives that have made disassembly difficult in the past. Here, the cell can be simply removed by hand, saving time and energy in the recycling process.
In the US, the government has acted too, pumping $15m into ReCell, an initiative composed of industry players and researchers, to develop novel ways of recycling batteries. In the UK a similar, multi-institutional initiative called ReLib has received substantial government backing to the same end. Both are focusing on ways to preserve the cathode in the recycling process. This is because the real value of a battery is accumulated in the raw elements and expertise that make up the cathode. Reselling this intact is much more profitable than breaking everything down to its elemental parts.
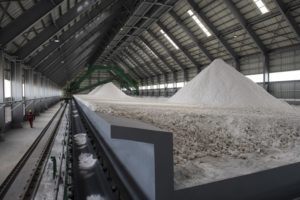
Source: nature.com
But even with the ability to extract the cathode without shredding the whole battery, there are still obstacles to rolling out this technique. One is simply the freight cost of transporting batteries to the plants for recycling, and another is that recycling plants may receive cathodes with very different makeups, some of which may be too difficult to separate. It’s important that regulators compel manufacturers to detail the contents of a cathode on the outside of the battery.
Taking a longer-term view, although we have use for recycled battery materials today, it’s very hard to know how useful the current stock of lithium units will be when they reach the end of their lives. In 15 years’ time, when today’s cars are coming off the roads for scrapping, the materials required for the manufacture of brand new cathodes may be very different from what we see today.
However, in spite of these obstacles, rather than seeing the massive growth of EVs as a problem, researchers see it as an opportunity—and this growth will bring to the lithium car battery recycling industry the economies of scale and profitability necessary to make it viable. Case in point; although the scrap value of lead is even lower than lithium, a viable recycling industry exists for traditional car batteries due to the sheer scale of usage, and because current EV batteries will outlive the cars they are housed in, they will likely go on to be used in other applications.
The International Energy Association places electric vehicles at the heart of its vision for net-zero emissions by 2050, suggesting they are here to stay. And while recycling lithium car batteries will not be enough on its own to satisfy the demand for raw materials to make new batteries, the industry can continue to reduce its environmental and social impact with concerted state and industry action.
For more information on the social and environmental impact of electric vehicles, contact one of our TRUE Advisors today. Additionally, subscribe to the RTS blog for more news and insights on sustainability.